Quality: Automotive Business
Our Approach
We believe that the foundation of SUBARU's “Enjoyment and Peace of Mind” is quality. Under our management philosophy that “the customer comes first” and to ensure that we become a company that resonates with and inspires trust in our customers, with “quality first” as our slogan, we are actively working to provide high-quality products and services that will impress our customers in all processes, from the product planning stage to procurement of parts from business partners, manufacturing and shipping at factories, and after-sales service. In order for SUBARU to continue to be the brand of choice for “Enjoyment and Peace of Mind” in the midst of the once-in-a-century period of major transformation in automotive manufacturing, it is essential to meet the expectations and trust that customers place in SUBARU with regard to the quality of our products.
In addition, our affiliates companies in Japan and overseas also practice quality control in their respective lines of business under a “quality-first” mindset.
Quality Policy
At SUBARU, quality is our highest priority as we earn the trust of our customers.
- We will deliver long-lasting products that our customers can use with peace of mind.
- We will continually improve our products and services by always listening closely to our customers’ voice.
- We will be a good corporate citizen in all markets where we do business by ensuring compliance with all internal rules, local laws, regulations and social norms.
Management System
In order to deliver high quality products to our customers, we believe it is important for each and every employee to work with an awareness of quality. SUBARU has established and is operating a quality management system (QMS) based on our Quality Policy and ISO 9001 standards. In addition, the Chief General Manager of the Quality Assurance Division has been appointed as the Chief Quality Officer (CQO) to oversee quality within SUBARU. Responsible parties at each department discuss quality issues under the CQO and promote quality improvement.
Quality Management System
SUBARU established the Automotive Business Quality Manual in 1995 as a guideline for quality management, and has established and operates a quality management system (QMS) based on the stipulations of this manual. We aim to improve quality and customer satisfaction by assuring that products will comply with both customer requirements and applicable statutory and regulatory requirements, as well as by improving our operations.
This Automotive Business Quality Manual is based on ISO 9001, a standard we have been consistently certified with since 2006.
Quality Management Cycle
Quality Improvement Committee
The Quality Improvement Committee is the highest body for promoting quality improvement and is attended by responsible persons in planning, development, procurement, manufacturing, sales, customer service, quality assurance, and other departments. Chaired by the Chief General Manager of the Quality Assurance Division, who is also the CQO, the committee meets monthly in principle to discuss all quality issues related to all operations in the Automotive Business Unit. In addition to the above-mentioned departments, the North America Quality Improvement Committee meets on a semi-annual basis to discuss issues related to the North American market, and includes representatives from dealerships in the United States and Canada, as well as SUBARU’s North America plants.
Development Quality Assurance System
In order to deliver quality products to our customers, it is of utmost importance to improve quality at the point of development. To this end, SUBARU launched its Quality Enhancement in 2018, and has been taking action in three areas: thorough implementation of a “Quality-First” mindset and reinforcement of organizational efforts and structure, Execution Quality enhancement, and Innate Quality enhancement. In particular, we are strengthening our Innate Quality enhancement activities and are working to ensure quality throughout all processes, from the initial planning and conceptualization stages to development, design, production preparation, and distribution. We have compiled a database of defects that have occurred in the market in the past, and we conduct general inspections to ensure that measures to prevent their recurrence are incorporated into the vehicles we develop. We also identify newly adopted parts and changes from vehicles produced in the past to prevent defects before they occur. In addition, the quality responsibilities of persons responsible for new vehicle development have been clarified and their authority has been strengthened. Furthermore, the development process has been changed to prioritize stage gate management of quality targets to enhance Innate Quality.
Market Quality Improvement System
The SUBARU Group has established a quality improvement system with the Quality Assurance Division at the heart of efforts in order to analyze after-sales quality defects and customer requests to rapidly take measures and achieve higher-quality product development and production. Based on customers’ opinions collected from around the world, SUBARU works with the relevant in-house departments and suppliers in identifying quality issues, investigating their cause, and planning countermeasures.
In January 2021, we established FAST (Fast Action & Solution Team), a North American quality improvement team where quality assurance and development units at local affiliated companies in the U.S. work together with service units at dealerships in the U.S. and Canada. By strengthening cooperation between departments, immediate decisions can be made on-site, and market demands can be met more speedily.
Quality Improvement System
Structure of the FAST North American Quality Improvement Team
Collaborative System with Business Partners
In order to maintain and improve the quality of SUBARU vehicles, it is extremely important to ensure the quality of externally purchased parts. Therefore, we are engaged in unified efforts with our business partners to ensure the quality of externally manufactured parts.
We have compiled standards and rules for building and ensuring stable quality into a manual, and by rolling it out to all of our business partners and working to ensure that everyone understands and adheres to it, we are building a foundation on which both sides can work together based on a common understanding. In addition, we hold briefing sessions on our Quality Policy for business partners at the beginning of each fiscal year to share information about quality-related situations. We have set quality targets and key quality indicators, and we present quality improvement measures, key points for enhancing quality, and other information as concretely as possible. Furthermore, by following the Advanced Product Quality Planning (APQP) process, our activities also encourage our business partners to make their own improvements, contributing to overall quality improvement.
In recent years, where the external environment has become extremely uncertain, parts supplies issues have arisen due to large-scale natural disasters and shifting world affairs. Amid this situation, we have also established support systems for our business partners in order to help quickly restore parts supplies in the event of an emergency.
Approach to Risks in Quality
Quality is an important element directly related to the survival of a company. While providing high-quality products enhances the credibility of the SUBARU brand, defects that reach the market bring us face-to-face with the risk of loss of customer confidence, a risk that can cause tremendous damage to corporate finances and reputation. Therefore, it is essential to continuously maintain and improve quality, and we believe that improving the quality of each employee's work will lead to the improvement of SUBARU's quality.
SUBARU conducts internal training on quality and holds events called Quality Caravans every year. Quality Caravans are conducted with the aim of fostering quality awareness through an accurate understanding of the current state of quality at SUBARU. In addition, internal audits are conducted by qualified employees to check that business is being conducted properly. We then undergo an audit by an external auditing organization to ensure our continued ISO 9001 certification.
As for our business partners, we support regular voluntary audits of quality assurance systems and quality management systems and provide advice from a third-party perspective. In addition to regular audits, SUBARU directly observes business partners’ manufacturing processes and production sites. Here, we conduct audits and process checkups on an ad-hoc basis, offer proposals for productivity improvement, and otherwise engage collaboratively to further improve quality.
Initiatives
Quality Assurance Training
Within the SUBARU Group, quality education is provided to all employees. Quality education is provided on an ongoing and regular basis tailored to employee knowledge and experience levels, including their year of entry into the Company and their position. This instills a customer-centric, quality-first awareness, educating each and every employee so that they put quality first in their actions.
We also recognize cases at our automotive manufacturing business units where a heightened focus on quality has resulted in the prevention of issues with a quality excellence award. Information on award recipients and their achievements is disseminated throughout SUBARU via the intranet and other platforms.
Global Quality Meeting
In order to steadily implement our quality-first philosophy, the SUBARU Group places great importance on dialogue with our dealerships around the world, who are in direct contact with our customers on a daily basis. Through technical liaison meetings held twice a year for the Japanese market, main dealerships service meetings held once or twice a year in overseas markets, and block conferences held in six regions,* we make decisions on matters such as optimum means of addressing quality problems that inconvenience our customers, while incorporating the views of dealerships. In FYE March 2025, these meetings are to be held in a combination of on-site and web-based sessions.
In addition, in order to listen to the voice of the market and speed up quality improvement, the Quality Improvement Committee, chaired by the Chief General Manager of the Quality Assurance Division, who is also the Chief Quality Officer (CQO), holds monthly meetings to discuss quality at the executive level in all departments. Furthermore, the North America Quality Improvement Committee, which is comprised of the North America CQO and heads of North American subsidiaries, focuses on quality in the North American market and is held several times a year.
- *
- Block conferences are held in a country in each of the six regions—the CIS, Central Europe, Northern Europe, Southern Europe, Oceania, and Central and South America. Their participants include representatives from dealerships’ service departments and expatriates working in the region.
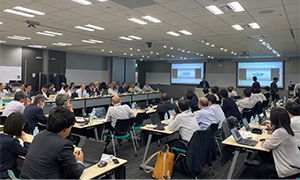
Quality Caravan
Since FYE March 2019, we have been holding an annual event called the Quality Caravan at all our business sites to inform participants of customer feedback and the quality status of SUBARU products. Our aim in doing so is to provide all employees with an accurate understanding of the current state of SUBARU and create an environment in which they are conscious of putting quality first at all times and approach their work in that mindset. In FYE March 2024, the caravan was held across a total of 40 days for all employees and Group company employees. We create and present videos that deepen understanding of the usage environment in the important market of North America, and provide straightforward explanations about recent quality concerns. The aim is to encourage each person to internalize the issues that impact our customers as their own, thereby fostering a customer-centric, quality-first mindset. Not only are we engaging more business partners in these events, but Subaru of Indiana Automotive, Inc., SUBARU’s production base in the U.S., has also been organizing events to raise global awareness of quality across the entire SUBARU Group.
Going forward, we will continue to engage in awareness activities, while enhancing the program and extending the duration, among other improvements.
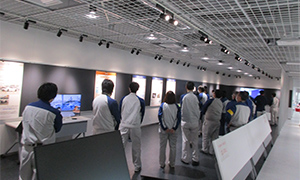
Pre-Shipment Inspection
At SUBARU, rigorous inspections are conducted before shipment to prevent any defects from leaving the facility. In 2018, the operation of vehicle inspections was spun off from the traditional manufacturing organization to form the Vehicle Inspection Department under the Quality Assurance Division in order to ensure thorough inspections from a customer perspective. In addition, we set up two new facilities for final vehicle inspections to establish an environment conducive to accurate inspections through clearly defined processes. The first facility started operations in August 2022, with the second becoming operational in August 2023. We provide environments with standardized lighting facilitating easier detection of anomalies, inspection processes at undercarriage using a lowered floor. With rigorous inspections in these environments, we aim to deliver high-quality products that customers can use with peace of mind.
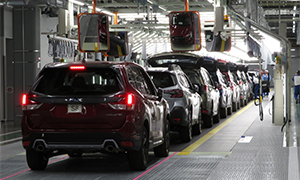
Investigation of Defective Parts
SUBARU set up the Quality Assurance (QA) Lab to investigate defective parts for the swift resolution of any issues that arise. In the event of a defect, development and manufacturing departments collaborate to determine causes and implement solutions. In cases where pinpointing the cause is especially difficult, the Quality Assurance Division expedites defect resolution by conducting independent analysis and investigation of defective parts in the QA Lab.
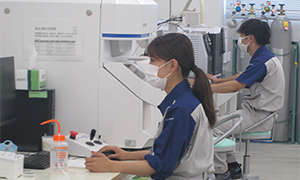
Response to Recalls
The SUBARU Group takes measures to cope with recalls in order to prevent accidents, in accordance with our highest priority placed on customer safety.
We have established the Recall Committee to determine specific measures to be taken in the event of product defects that can infringe on safety or laws and regulations. This committee is chaired by the Chief General Manager of the Quality Assurance Division, who is the CQO, and was established based on customer suggestions and defect information from around the world and in accordance with internal regulations. Any recalls are promptly reported to the relevant authorities. Affected customers are contacted by direct mail and other methods from our dealerships to encourage them to have their car repaired free of charge, with their safety and peace of mind as our top priority. We monitor the progress of market measures to ensure that improvements can be made quickly.
As of April 2024, SUBARU had no cases of violating laws and in-house regulations in regard to information provision on quality and safety.
At SUBARU, we are advancing “parts traceability” by linking the individual vehicle number with the individual part number to quickly and accurately identify vehicles equipped with defective parts. In the unlikely event of a recall, we are committed to minimizing any inconvenience to our customers through our efforts.
Recalls of SUBARU Cars
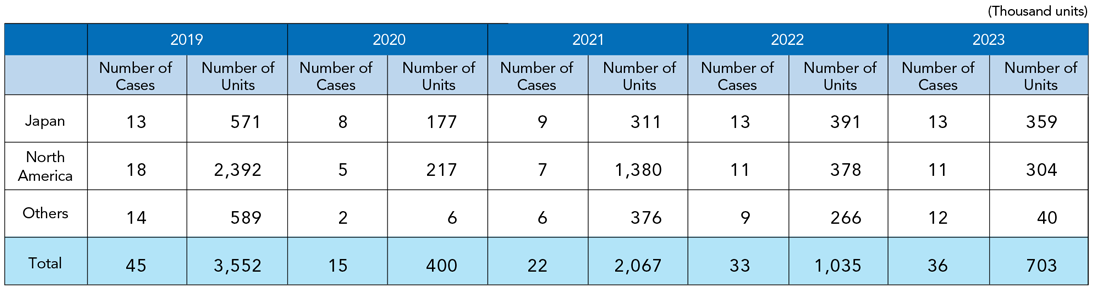
- *1
- Information presented is internal data and may differ from data published by the respective authorities.
- *2
- Identical recalls conducted across multiple countries/regions are combined to count as one recall.
- *3
- Number of recalls include those for OEM vehicles.
Takata Airbag Recall Progress
SUBARU’s recall progress related to the Takata airbag recall in the U.S. is among the highest in the industry.
Takata airbag recall progress in the U.S.
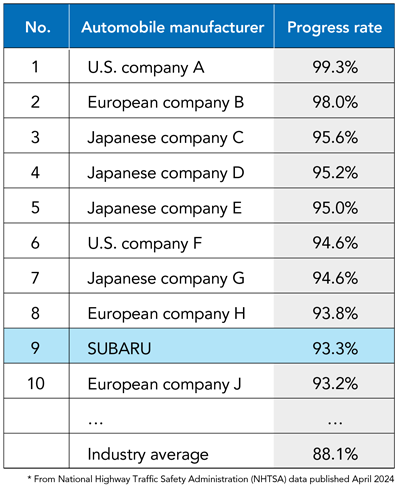