Achieving a Circular Economy
Our Approach
The SUBARU Group considers it very important for manufacturing companies to help realize a society where materials are recycled continuously and the sustainability of business is assured through recycling to maximize resource efficiency.
The SUBARU Group is working to the realize a recycling-oriented society and aims to achieve efficient resource recycling throughout the product life cycle, consistently achieving zero landfill at production sites in Japan and overseas, and taking the 3Rs—reduce, reuse, and recycle—to the next level.
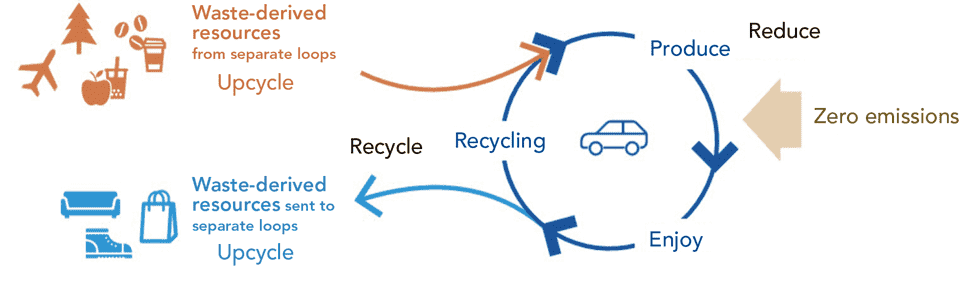
Management System
SUBARU’s Zero Emission Management Organization

Medium-Term Goals
Furthermore, we have set the target of proceeding with research and development with the goal of using recycled materials*5 for more than 25% of the plastics used in new models released worldwide by 2030 to help address the global waste plastic problem. To achieve this target, we are working to establish quality standards for recycled plastics and a raw material recovery scheme. Our production target has also been set as achieving zero emissions at production plants*4 in Japan and overseas (zero landfill waste either directly or indirectly).
Category | Target Year | Goal |
---|---|---|
Products | 2030 | ·Pursue research and development targeting the use of recycled materials*1 for more than 25% of the plastic used in new models*2 by 2030 ·Adopt CO2-free materials such as biomass plastic. ·Proactively adopt plastic materials*3 that have less environmental impact. |
Production | Zero emissions*4 at production plants in Japan and overseas*5 |
- *1
- Including material, chemical, and plastic recycling.
- *2
- Excluding models supplied by OEMs.
- *3
- Materials and suppliers with lower CO2 emissions and environmental pollution at the manufacturing stage.
- *4
- Final landfill rate of 0.5% or less.
- *5
- Parent company: Gunma Plant, Tokyo Office, Utsunomiya Plant; Subsidiaries: Fuji Machinery Co., Ltd., Kiryu Industrial Co., Ltd., Ichitan Co., Ltd., Subaru Logistics Co., Ltd., Yusoki Kogyo K.K., Subaru of Indiana Automotive, Inc.
Initiatives
SUBARU promotes vehicle manufacturing with recycling in mind to make effective use of limited resources, working on resource efficiency throughout the entire lifecycle of automobiles, from raw material procurement and manufacturing to disposal.
In addition to continuing to promote the use of recycled materials and push for zero landfill at production sites both in Japan and overseas, we are also advancing research on the use of diverse sustainable new materials and developing upcycled products using scrap materials.
Product Initiatives
Design for Recycling
SUBARU incorporates recyclability into its automobile design process to make effective use of limited resources.
Use of Recycled Materials
Utilizing Recycled Resins
To contribute to realizing a resource-recycling society and a decarbonized society, SUBARU is working to develop technologies to utilize recycled resins and biomass materials in place of the resins currently used in automobiles.
Examples of recycled resin use in the 2023 Crosstrek and Impreza
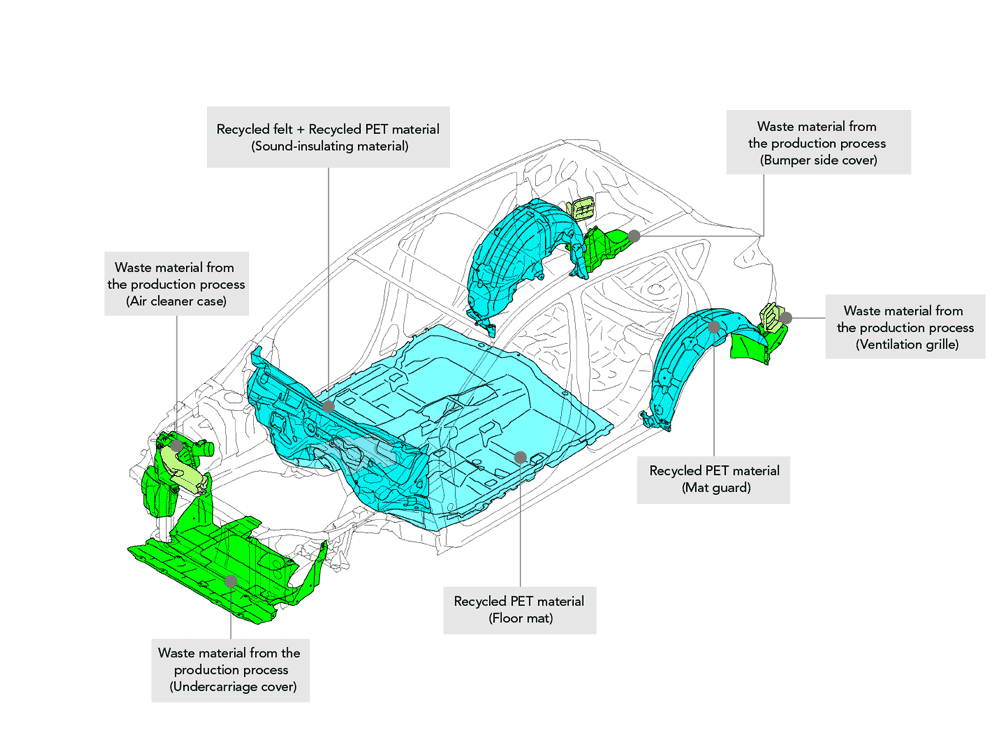
Utilization of recycled materials in floor mats (Subaru of America, Inc.)
Subaru of America, Inc. has developed environmentally friendly accessories, specifically floor mats made from materials recycled from marine debris. Both the surface and backing consist of 100% eco-friendly materials. In 2023, 164,000 units were sold.
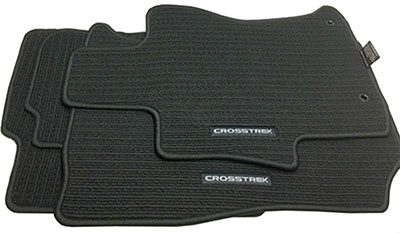
Recycling of Windshields (Subaru of America, Inc.)
The recycling of the films used in windshields has posed challenges. To address this, SUBARU has partnered with a processor capable of material recycling, leading to the successful recycling of over 7,000 windshields.
Upcycling Initiatives to Recycle Production Scrap Materials into New Goods
In the concept of upcycling, items that were once disposed of are transformed into products of attractive value. SUBARU is focusing on scrap materials generated in the manufacturing process to collaborate with peer companies and create new value beyond the boundaries of automobiles.
Aprons made from leftover cloth and cotton waste from factories (Takihyo Co., Ltd.)
SUBARU aims to enrich lifestyles and conserve the global environment through its goods. A direct outcome of connecting this idea to product development is our partnership with Takihyo Co., Ltd. to collect leftover cloth and cotton waste from factories and use the re-spun fabric to make aprons. These are designed with ample thought given to pocket location, combining design and environmental performance.
See the following link for product information:
https://onlineshop.subaru.jp/subaru/lifestyleitem/FHTK22002000(Japanese version only)
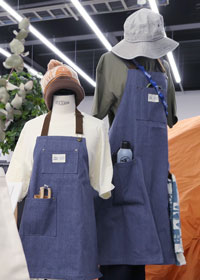
Eco-Friendly Shopping Bags Made from Leftover Fabric (TOYODA GOSEI Co., Ltd.)
SUBARU has created an eco-friendly bag (product name: Marche Bag) that is essential for everyday life by making use of scrap materials that would have been discarded during the production process of airbag fabric. As part of SUBARU's commitment to safety, Marche Bag uses a patented reflective material that glows in the dark, enhancing safety on roads at night. Furthermore, we have used ergonomic theory to adjust the thickness of the handle so that even when carrying heavy loads, the weight does not put a strain on the arms.
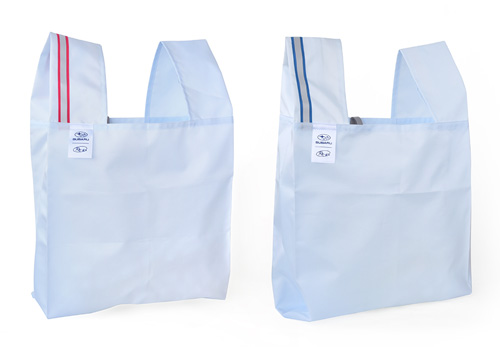
Key Straps Made from Upcycled Fishing Net Waste (CANVAS CO., LTD.’s PoLER brand)
SUBARU collaborated with CANVAS CO., LTD. to address marine pollution by producing key straps made from discarded fishing nets. Portions of the straps are made from recycled fishing nets processed into a material called reamide.
By using this reamide derived from used fishing nets, SUBARU contributes to resolving the marine debris problem while also reducing CO2 emissions compared to the use of virgin materials.
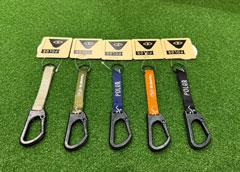
Development of Sustainable Materials
Research on Plant-derived Materials such as Food Processing Residue
Mixing post-juicing fruit residues and thinned wood into resins allows us to cut down on petroleum-based resin use. We are effectively utilizing plant-derived waste as raw materials for automobile parts, which until now had to be incinerated in food processing and other areas, making it a social issue. Through this utilization, we are not only recycling resources, but also promoting research so that people can enjoy the natural feel and narrative of sustainable materials with peace of mind.
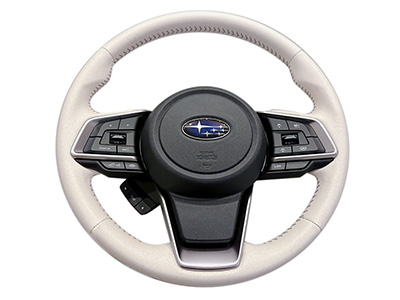
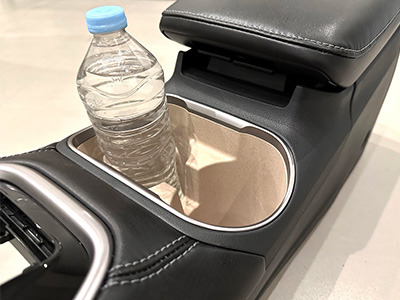
Research on High-performance Recycled Materials
SUBARU has been studying the reuse of waste generated in the product manufacturing process from various angles. One example comes from a collaboration with SUBARU’s Team SDA* Engineering, the team leading our entry in the Super Taikyu Series of races. Here, we have taken a carbon fiber bonnet, made of carbon fiber recycled from composite waste generated in aircraft parts manufacturing, using the bonnet in the SUBARU BRZ used in competition. This has reduced not only the vehicle’s weight but also its environmental impact.
In addition, the development of a material using recycled carbon fiber that comes as close as possible to the material properties of the original carbon fiber and the construction of an optimal design method using recycled carbon fiber composite materials became the topic of joint collaboration between SUBARU and other institutions to achieve reuse in aircraft parts, which are subjected to more rigorous conditions. It resulted in a joint proposal, the research on the technology of continuous production of recycled carbon fiber and its application to aircraft, which was adopted as a New Energy and Industrial Technology Development Organization (NEDO) research program.
- *
- Acronym for SUBARU Driving Academy, a human resources development initiative to raise driving and evaluation skills of SUBARU engineers
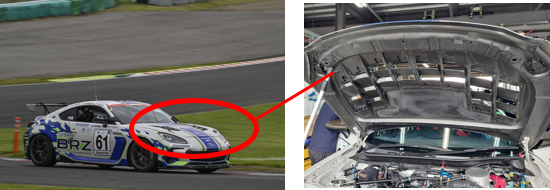
Site Initiatives
Waste generation in FYE March 2024 increased 10,105 tons year on year due to increased production volume. As waste is also an important resource, we have maintained zero emissions* of waste since FYE March 2015 through maximum recovery and recycling and proper treatment of waste generated. As part of its measures to deal with waste plastic, SUBARU has begun exploring waste plastic material recycling, including the reuse in automotive parts and other applications of reject bumpers from the manufacturing process.
- *
- A system in which waste and by-products generated in one industry are utilized as resources by other industries, resulting in no waste discharge. This concept was proposed by the United Nations University in 1994.
Primary waste products and their recycled products
Primary Waste Product | Primary Recycled Product |
---|---|
Wastewater treatment plant sludge | Raw material for cement |
Paint sludge | Iron-making reducer |
Waste plastics (solid fuels, etc.) | Refuse paper and plastic fuel (RPF) |
Paper waste | Recycled paper, RPF, etc. |
Waste Generation
Scope
- SUBARU:
- Gunma Plant, Tokyo Office, Utsunomiya Plant, Handa Plant, Handa West Plant, Ebisu Subaru Building, Accessory Center, SUBARU Training Center
- Group companies in Japan:
-
Yusoki Kogyo K.K., Fuji Machinery Co., Ltd., Ichitan Co., Ltd., Kiryu Industrial Co., Ltd., Subaru Logistics Co., Ltd.
- Group companies overseas:
-
Subaru of Indiana Automotive, Inc., Subaru of America, Inc., Subaru Canada, Inc., Subaru Research & Development, Inc.
Amount of Waste Generated and Processed
- Based on aggregation of data from Gunma Plant, Tokyo Office, Utsunomiya Plant
- Note:
- Waste is not disposed of in a landfill after external intermediate processing.
Recycling of aluminum chips
Initiatives and Achievements for Circular Use of Waste Plastic
In FYE March 2024, waste plastic accounted for 2.3% of the SUBARU Group’s waste generation. Although the amount of waste plastic generated is a small percentage of total waste generated, SUBARU will work to improve the waste plastic recycling rate and actively pursue circular use of waste plastic, including considering a switch from thermal to material and chemical recycling methods.
FYE March 2024 SUBARU waste plastic recycling rate and recycling treatment breakdown
Scope of aggregation
- SUBARU:
- Gunma Plant, Tokyo Office, Utsunomiya Plant, Handa Plant, Handa West Plant, Ebisu Subaru Building, Accessory Center, SUBARU Training Center
Employee Participation in Recycling Waste (Subaru of Indiana Automotive, Inc.)
Every year, Subaru of Indiana Automotive, Inc. provides support for employees to bring in waste from their homes for proper recycling and disposal. In 2023, we recycled approximately 31,000 pounds of hazardous waste, from oil and paint to electronic equipment and pharmaceuticals.
Sales Initiatives
Zero Emissions of Waste from SUBARU Dealerships in Japan
Dealerships in Japan are committed to the proper management of waste generated from their business activities and to recycling to achieve zero emissions in Japan. In FYE March 2024, these initiatives resulted in the collection of 26,153 used bumpers, 145,347 lead batteries (containing 1,986 tons of lead material), 5,018 kL of oil, and 190,819 tires.
Zero emission initiatives led by dealerships, which work most closely with customers, are activities that will contribute more directly to environmental conservation in local communities. The initiatives are expected to help promote proper processing, recycling, and the effective use of resources.
Recycling of used bumpers
Recycling of Waste Oil
Waste oil generated at SUBARU dealerships in Japan during oil changes is recycled as recycled fuel oil through SUBARU’s zero waste emissions scheme. Flower farmers in Yamagata Prefecture grow beautiful poinsettia and cyclamen every year using this recycled fuel oil to heat their greenhouses.
Waste cooking oil discharged by the operator of the employee cafeteria at the Subaru Logistics Co., Ltd. headquarters is recycled under the Fry To Fly Project scheme, which aims to convert the oil into sustainable aviation fuel (SAF). At present, this oil is recycled as biodiesel fuel, with plans to recycle it as SAF starting in 2024.
Proper Processing of End-of-life Vehicles
SUBARU is participating and collaborating actively in the building of an automotive recycling system to reduce the environmental impact of end-of-life vehicles. SUBARU is also focusing on promoting the development of easy-to-recycle vehicles, and collaborates with its dealerships nationwide by jointly operating an automotive recycling system aimed at promoting the proper processing and raising the recycling rate of ASR, airbags, and CFCs.
In FYE March 2024, the ASR recycling rate was 96.6%, achieving the legal target of 70% for FYE March 2016 and thereafter. The airbag recycling rate was 96.6%, exceeding the legal target of 85%, and all CFCs recovered were processed properly.
Detailed information on the level of progress with these recycling initiatives and SUBARU’s other activities based on the Act on Recycling, etc. of End-of-Life Vehicles is disclosed separately on the web page indicated below.
- About the Act on Recycling, etc. of End-of-Life Vehicles (Japanese version only)
- Automobile shredder residue Recycling Promotion Team (ART) (Japanese version only)
Automobile Recycling Process
Act on Recycling, etc. of End-of-Life Vehicles
Under the Act on Recycling, etc. of End-of-Life Vehicles of Japan, car manufacturers are required to fully recover and properly recycle automotive shredder residue (ASR), airbags, and chlorofluorocarbons (CFCs) from their end-of-life vehicles.
SUBARU has been promoting the smooth, proper, and efficient recycling of ASR through the Automobile Shredder Residue Recycling Promotion Team (ART).*1 We also ensure proper processing of airbags and CFCs through operations of Japan Auto Recycling Partnership Ltd., established jointly with Japanese automakers and importers.
- *1
- A team to promote the recycling of ASR, organized by 12 domestic automobile manufacturers and importers in 2003. The team plans the smooth, proper, and efficient recycling of ASR, a waste product that is classified as one of the Parts Specified for Recycling as defined by the Act on Recycling, etc. of End-of-Life Vehicles and required to be recycled under the law.
Use of Rebuilt Items (Subaru of America, Inc.)
In the U.S., to achieve a recycling-oriented society, SUBARU is working on the use of rebuilt items*2 for replacing large components such as engines and transmissions. This initiative aims to reduce environmental impact and lower costs for customers by extracting and reusing all available seals and gaskets from replacement parts.
- *2
- Repair parts such as engines, etc., for which consumable parts are replaced and usable parts are reused in accordance with inspection standards.
Initiatives at the Headquarters Building (Subaru of America, Inc.)
The SOA headquarters building has acquired silver LEED certification, and the company is making efforts to use recycled materials, such as using recycled wood for the lobby and café wall decorations and using recycled materials for some of the employee workstations and carpets. Many recycled materials are used in the construction of the entire building, from the steel frame and metal parts to the precast panels and finishes.
Eco Friendly Retailers (Subaru of America, Inc.)
SOA has launched the Eco-Friendly Program in collaboration with its retailers across the U.S. to promote the reduction of environmental impacts related to energy, water, and waste. To obtain certification under the program, retailers must meet standards in areas such as energy efficiency and recycling. As of 2023, 255 retailers, representing 40% of the program, have participated. In 2023, as part of the resource circulation initiatives under the program, approximately 20 tons of waste generated by the dealerships was processed for recycling.
Zero Landfill Waste Joint Initiative in U.S. National Parks (Subaru of America, Inc.)
SOA has leveraged its expertise in zero landfill waste at Subaru of Indiana Automotive, Inc. (SIA), collaborating with suppliers, the National Parks Conservation Association, the National Park Service, and others since 2015 to reduce waste from three national parks: Yosemite National Park (California), Denali National Park and Preserve (Alaska), and Grand Teton National Park (Wyoming). To date, over 10,000 tons of waste has been diverted from landfills to recycling and composting. SOA received the Silver Halo Award and the Corporate Stewardship Award in 2020 in recognition of zero landfill initiatives in national parks. In October 2023, the National Parks Conservation Association (NPCA) presented the Centennial Leadership Award to SOA in recognition of its ongoing commitment and support for national parks in the United States.
Subaru Park Zero Landfill (Subaru of America, Inc.)
Subaru Park, a soccer stadium in Chester, Delaware County, Pennsylvania, supported by Subaru of America, Inc, has become the first Major League Soccer Stadium to achieve zero-landfill status since 2021. In 2023, approximately 270 tons of waste generated at Subaru Park was processed for recycling.
E-waste (Subaru of America, Inc.)
One of Subaru of America, Inc.’s initiatives is to appropriately recycle e-waste (waste from electric and electronic devices) from employee homes. In its 2023 Earth Day event, approximately 500kg of e-waste was collected and processed for recycling.
Sustainable Subaru Gear (Subaru of America, Inc.)
Subaru of America, Inc. works with Staples Corporate to provide environmentally friendly SUBARU-branded clothing and products for people and their pets, and helps reduce environmental impact by utilizing 100% recycled plastic bags and recyclable shipping boxes. In 2023, more environmentally friendly products were added, accounting for more than 40% of the total products offered.
In addition, Staples Corporate continued its partnership with EcoVadis, a sustainability rating agency, and maintained its Silver status, ranking in the top 25% of companies and industries evaluated. Staples Corporate also launched a responsible procurement in 2023, which is driving continuous improvement in the supply chain.
Zero landfill initiative at Subaru of Mississauga
In collaboration with the local business U-PAK DISPOSALS, approximately 40,000 tons of waste was collected and processed for recycling for the year through the Energy from Waste program.
Food Waste Reduction Activities (Subaru of America, Inc.)
SOA has partnered with hospitality partner Eurest to strategically place scrap containers throughout the office to collect employees' food waste. In FYE March 2024, approximately 20 tons of food waste was repurposed as animal feed and compost.
Initiatives for Environmental Conservation Education (Subaru Canada, Inc.)
Subaru Canada, Inc. has organized events and activities for e-Waste Week to promote awareness and education about the importance of environmental conservation, including major spring cleaning. For Clean Air Day in Canada, Subaru Canada also held a breakfast meeting and a unique commuting challenge for all employees who walk/run to work or otherwise commute by bicycle, by public transport, or by carpooling.
Logistics Initiatives
Logistics
Reuse of Packaging Materials
Subaru Logistics Co., Ltd., which handles packaging and transport for complete knockdown (CKD) parts of SUBARU automobiles, has been actively working on reducing its environmental impact, focusing on the reuse of packaging materials.
In FYE March 2024, the amount of packaging materials reused increased 20% year on year to 1,023 tons, a vehicle intensity of 2.8 kg. This was due to a significant increase in the number of packaged units and the full-scale mass production of the new Impreza, which has a high reusable material adoption rate.
Going forward, we will continue to promote the reuse of materials to reduce environmental impact.
(FYE March)
2019 | 2020 | 2021 | 2022 | 2023 | 2024 | |
---|---|---|---|---|---|---|
Amount reused (t) | 776 | 1,020 | 661 | 786 | 852 | 1,023 |
Intensity (kg/vehicle) | 2.1 | 2.8 | 2.4 | 2.7 | 2.8 | 2.8 |
Reduction of Wrapping Materials on Bumpers for U.S. Market
At Subaru of America, Inc., non-colored bumpers imported from Japan are re-wrapped for protection during transport within the U.S. In FYE March 2021, we have launched an initiative to remove the need for re-wrapping in the U.S. by applying high-strength wrapping material with high shape stability before export from Japan.
Distribution Centers (Subaru of America, Inc.)
Subaru of America, Inc.’s regional distribution centers use returnable containers to reduce the amount of cardboard and wood used when transporting parts. In 2023, a total of 2,131 pounds of waste was recycled at all locations, including wooden pallets and electronic waste, for a total recycling rate of 85.3%.
Promoting Environmentally Friendly Packaging Materials
The company’s Parts Distribution Center is progressing with environmentally friendly initiatives on packaging materials and began exploring a range of measures in FYE March 2022, namely switching from cardboard to paper packaging for improved transport efficiency, use of packaging materials with 10% content of biomass plastic material, and switching from resin to cardboard pallets.
The Parts Distribution Center, has successfully eliminated plastic use and improved workability through the use of paper cushioning and packaging materials. After studying the possibility of switching from wood to cardboard as a packaging material for large parts such as bumpers, engines, and transmissions, we adopted cardboard from FYE March 2024. In addition, from FYE March 2024, we are working to eliminate excessive quality in plastic packaging materials (e.g., eliminating, reducing size of, and adjusting thickness of materials) in order to eliminate plastic use. We are also promoting environmentally friendly initiatives in packaging materials.
Procurement Initiatives
SUBARU reuses remnant materials and scrap generated during the production of automobiles as well as end-of-life products that have been collected and other reusables as resources for materials, such as iron, aluminum, and plastics, which account for a large proportion of materials used in making an automobile. Through these efforts, we are promoting closed-loop recycling* to reduce natural resource consumption and waste generation.
- *
- A method by which waste and scrap generated during production along with end-of-life products are recycled as materials for parts of the same quality and then reused to make products of the same kind.
Raw Materials Used in Automobiles in FYE March 2024 | Recycling Method | |
---|---|---|
Iron | 619,057t | Delivered to dealerships in the form of iron scrap for reuse |
Aluminum | 30,976t | Re-melted at plants and reused almost entirely |
Plastics | 24,872t | Crushed again at plants and reused partially |